Before 2012, the extent of my manufacturing knowledge came from Michael Shuman’s book The Miracle: The Epic Story of Asia’s Quest for Wealth (highly recommended). After moving to New York City to join a hardware startup, I began to slowly educate myself about what goes into making physical objects. Since joining Keen Home, I’m closer to the production side than ever before and I’m learning new manufacturing techniques faster than I can keep up. It’s a good problem to have — understanding manufacturing and what goes into building hardware is essential to understanding your products and providing great customer experiences.
Understanding manufacturing and what goes into building hardware is essential to understanding your products…
One process that has stuck out the most is electrical discharge machining, or EDM. It’s amazing and one of the most unusual methods I’ve seen. Our co-founder Will McLeod walked me through it.
What is EDM?
In manufacturing, EDM is a machining process used with hard metals or for designs that would be very difficult to achieve with traditional techniques. With EDM a desired shape is created using electrical discharges or “sparks”. We’ll explain what all of that means, but first let’s talk about the equipment that is involved.
In a typical EDM process, material is removed from metal by rapidly repeating current discharges between two electrodes. There are three main components:
- The tool-electrode (or simply the “tool” or “electrode”)
- The workpiece-electrode (the “workpiece”)
- Dielectric liquid
The electrode is in the shape or design you are trying to manufacture, and both it and the workpiece are made from conductive material such as copper. A positive electrical charge is applied to the electrode while a negative charge is applied to the workpiece you are shaping. The two pieces are separated by the dielectric liquid, a non-conductive electrical insulator that prevents the electric current created between them from expanding beyond the work area.
There are two main types of EDM:
Die-sink EDM
Die-sink machines work by submerging the negatively-charged workpiece in dielectric liquid and lowering the positively charged electrode on top of it. The electrode is quickly lowered and raised above the workpiece, never touching it but creating a powerful electrical current — called a spark channel — that burns the design of the electrode into the workpiece. The dielectric liquid flushes out the burnt pieces of metal, leaving behind the desired design.
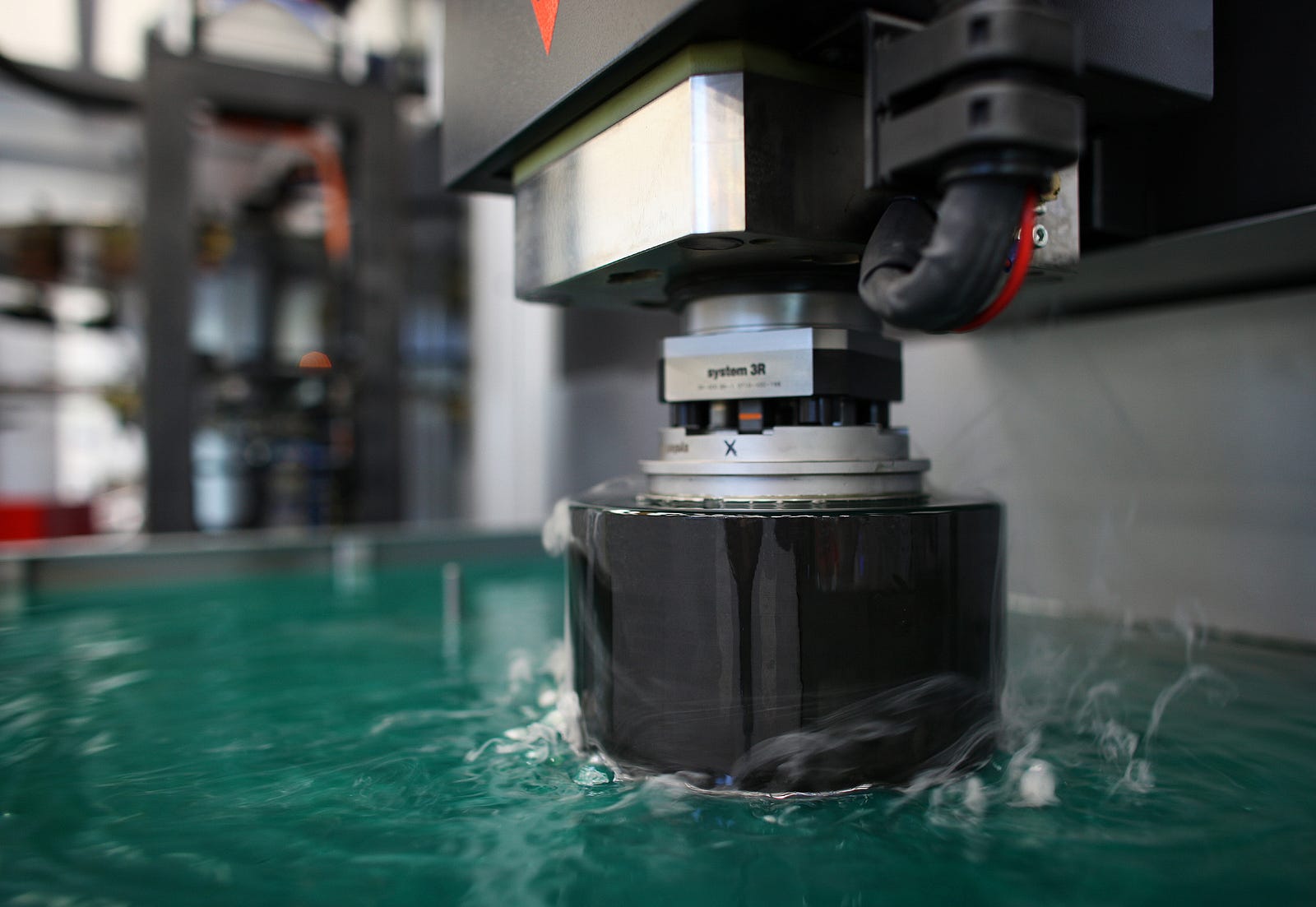
Here’s a video that I found helpful when researching the process of die-sink EDM:
Die-sink EDM
Wire-cut machines use a hair-thin wire as the tool-electrode. The same positive charge that is run through the electrode in a die-sink process is run through the wire, but unlike die-sinking, the wire precisely cuts away microscopic bits of material from the workpiece rather than burning them away from on top of it. To prevent the wire from eroding, it is wound around two spools that constantly wind it up to change the area of the wire making contact with the workpiece. Dielectric liquid is run across the wire and workpiece, flushing away cut material and keeping the current generated between the wire-electrode and the workpiece from burning other areas of the piece.
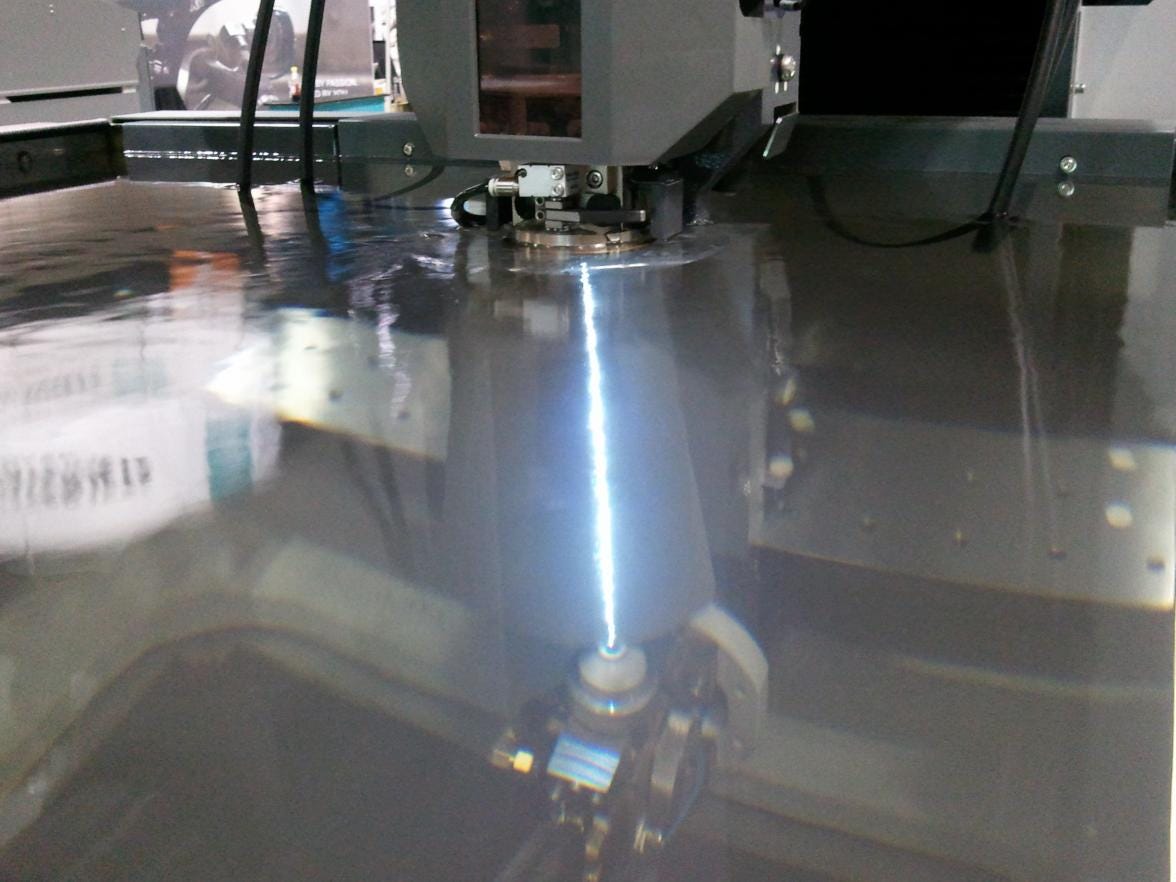
Here’s a video from a wire EDM company that explains the process well:
So which of these do we use?
Both.
Each Smart Vent cover has the Keen Home logo imprinted on the outside. To get the logo on the vents, we needed to create a mold to put it there. Creating this mold (called a “tool”) is where die-sink EDM comes into play. Our factory first machines an electrode to create a positive mold of the logo. We then use the electrode to create a negative, which we can use to manufacture more positives for the mass production process.
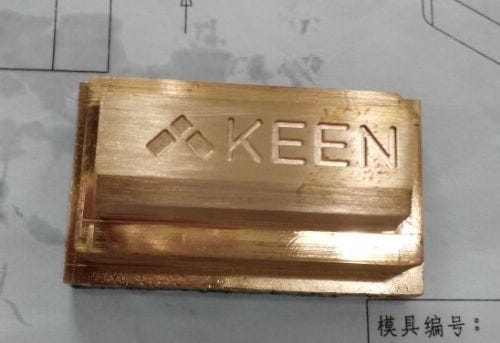
Wire-cut EDM is our go-to manufacturing process for prototypes of our aluminum airfoil vein. We take a block of aluminum, drill a hole down the center, and drop the EDM wire into the hole. The wire-cut machine then cuts the veins according to uploaded computer numerical control (CNC) models. The end results are super precisely machined veins that are significantly less expensive and time consuming to produce than through a traditional casting process.

While in our case EDM is primarily used for prototyping and creating tools for mass production, it’s can be extremely useful for a variety of manufacturing needs. Whether creating complex shapes, producing pieces with thin walls, or working with extremely tough material, it may be your best option for getting extremely high quality results. If you’re interested in incorporating EDM into your manufacturing process and need help finding an service provider, ThomasNet has a comprehensive list of manufacturers throughout the US.