Most people have no idea what goes into making the products they know and love. As a company dedicated to improving lives through hardware, we want to change that. In this 4 part series, we’re pulling back the curtain on our manufacturing process and giving an inside look into what goes into building the Smart Vent. Check out the other blog posts here: Good, Fast, Cheap -- Choose Two, Why China is Essential, and Batteries Included.
By the second week of our manufacturing trip, we were ready to bring our first off-the-line models of the Smart Vent to our massive RF testing chamber. We’d been testing at every step of the process, but each time you change how your parts are made, tests need to start over. Moving to mass manufacturing means a whole new set of tests to ensure everything carried over.
Each time you change how your parts are made, tests need to start over.
After weeks and weeks of design testing before this most recent trip to China, the tests this time around were to achieve FCC certification. This certification is essential to prove that our product doesn’t generate any harmful interference that might interrupt normal functions of other networks like WiFi. We also tested range and antenna strength under hundreds different variations of materials, angles, power levels and even in and out of disembodied HVAC ducts. While many of these tests have no regulatory mandate, they are important to ensure our product will work in far more homes than we could reasonably test in.
We conducted our testing in a 3 meter wireless RF chamber like the one pictured at the start of this post. The white panels and blue forest of cones are made from specialized foam that is excellent at absorbing radio signals. This ensures that no errant signals bounce around the room and make it look like our radios are stronger or weaker than they actually are.
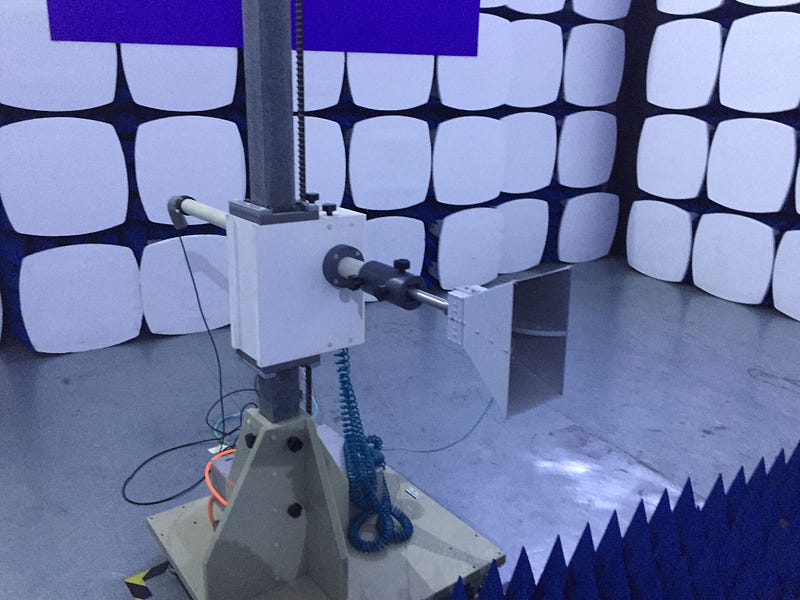
We use a radio antenna like the one above to precisely measure radio signal strength over a range of frequencies. We’re not just checking for strong signals, we also need clean ones. Our radios are within the 2.4 GHz band and the tests we run ensure that the Smart Vent doesn’t emit signals in other bands that might interfere with your radio, TV, cellphone, or other wireless devices. We tested the vents in a duct facing the antenna, facing away from it, and just about every angle in between.
During this trip we also tested variations of steel reinforced vent covers, which make them safe for floor use. These vent covers have been designed to hold hundreds of pounds on a small area, just in case you happen to land a kitchen chair leg directly on one. Testing these with the Smart Vents in an RF chamber is important because of the potential for the metal reinforcement to interfere with radio signals. If we found that our design obstructed signal strength, we would need to redesign the vent covers. Thankfully, they passed with flying colors.
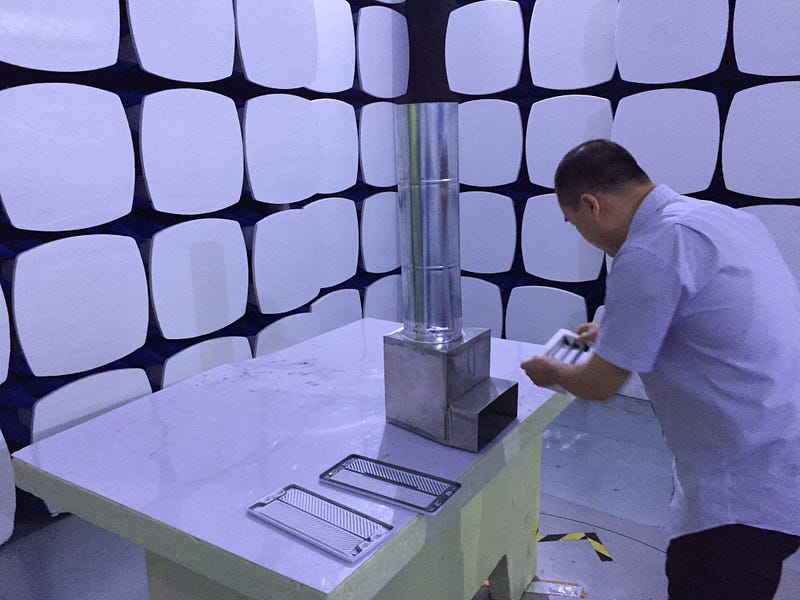
Each major change to the hardware comes with another battery of radio tests to verify performance. You are probably starting to notice a trend: every little piece, every single detail of any piece of hardware — let alone the Smart Vent — needs to be tested thoroughly to ensure great quality, necessary certification, and a memorable customer experience. For us, these are the most important pieces of the manufacturing puzzle; anyone can manufacture an object, but it takes commitment and testing to produce a truly outstanding product.
It takes commitment and testing to produce a truly outstanding product.
After two weeks of quality obsessed specification, testing and compliance work, we said our goodbyes to our manufacturing team. We had finally finished adjusting to the 12 hour time zone flip when we boarded our early morning flight back to NYC.
We’ve barely had time to adjust to being home, but already the team is heading back to do it all over again in the next phase of high quality manufacturing. This trip will be focused on quality assuring our smart hub hardware (more on that in coming posts), tooling up the remaining vent sizes (we started with the most common, 4”x10”), and the last round of quality tweaks before mass manufacturing.
Test, test, and test again… all in the name of comfort.
This post was written by Will McLeod, Keen Home’s Technical Co-Founder on June 3, 2015.